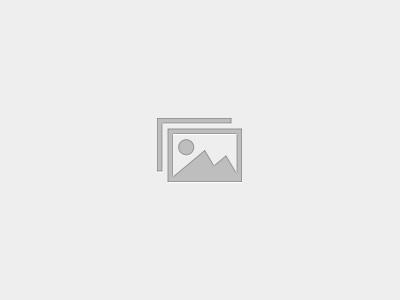
Working at Heights Training
Duration:2 days Description
The
Working at Heights course is designed to prevent falls in the workplace. This
course allows ensures the safety of individuals working in areas such as roof
works, scaffolding, ladders and more. This course is aimed at providing
candidates with the necessary skills and knowledge to undertake work at heights
safely and competently, covering selection, inspection and safe use of
equipment; risk management; and requirements of relevant Australian Standards,
company procedures and legislation. The course practically applies these and
other safe work practices.
What You Will Learn
The
aim of the course is to provide learners with the requisite WAH knowledge to
manage work-at-height activities, so that work can be carried out safely. At
the end of the course, the learner shall be able to:
·
Identify, explain and apply the relevant Workplace
Safety and Health (WSH) Legislations / Approved Code of Practice / Singapore
Standards applicable to Work- at-Heights (WAH)
·
Identify and explain the Roles &
Responsibilities of stakeholders, competent
and responsible persons
·
Identify hazards, evaluate the risk, and implement
control measures for WAH activities
·
Review the necessary fall
preventive / protective control measures for
safe execution of WAH activities
·
Establish, evaluate, review and implement a Fall
Prevention Plan
·
Establish and implement a system for an effective
monitoring and control of WAH risks
·
Demonstrate competency in donning,
checking and correcting of Individual Fall
Protection Equipment and Responding to a fall
emergency
Who Should Attend:
Persons involved in supervision, assessment and/or management of WAH
activities.
Course Outline
· Legal
requirements, Approved Code of Practice and Standards for WAH
· Roles and
Responsibilities of various stakeholders
· Risk Management
· Fall Control Measures
· Fall Prevention Plan
· WAH Implementation
and Monitoring Program
·
Demonstration and Practical Performance
Elevated
Work Platforms (EWP)
·
planning and risk
management;
·
applicable legislations and standards;
·
EWP types,
·
characteristics and uses;
·
inspection,
·
maintenance and testing of the EWP;
·
appropriate PPE;
·
correct set up;
·
safe and efficient operation techniques;
·
spotting;
·
shut-down and stowage procedures and associated paperwork.